Leroy Merlin automatisiert sein Lager zugunsten seiner Teams und der Leistung
- Supply Chain
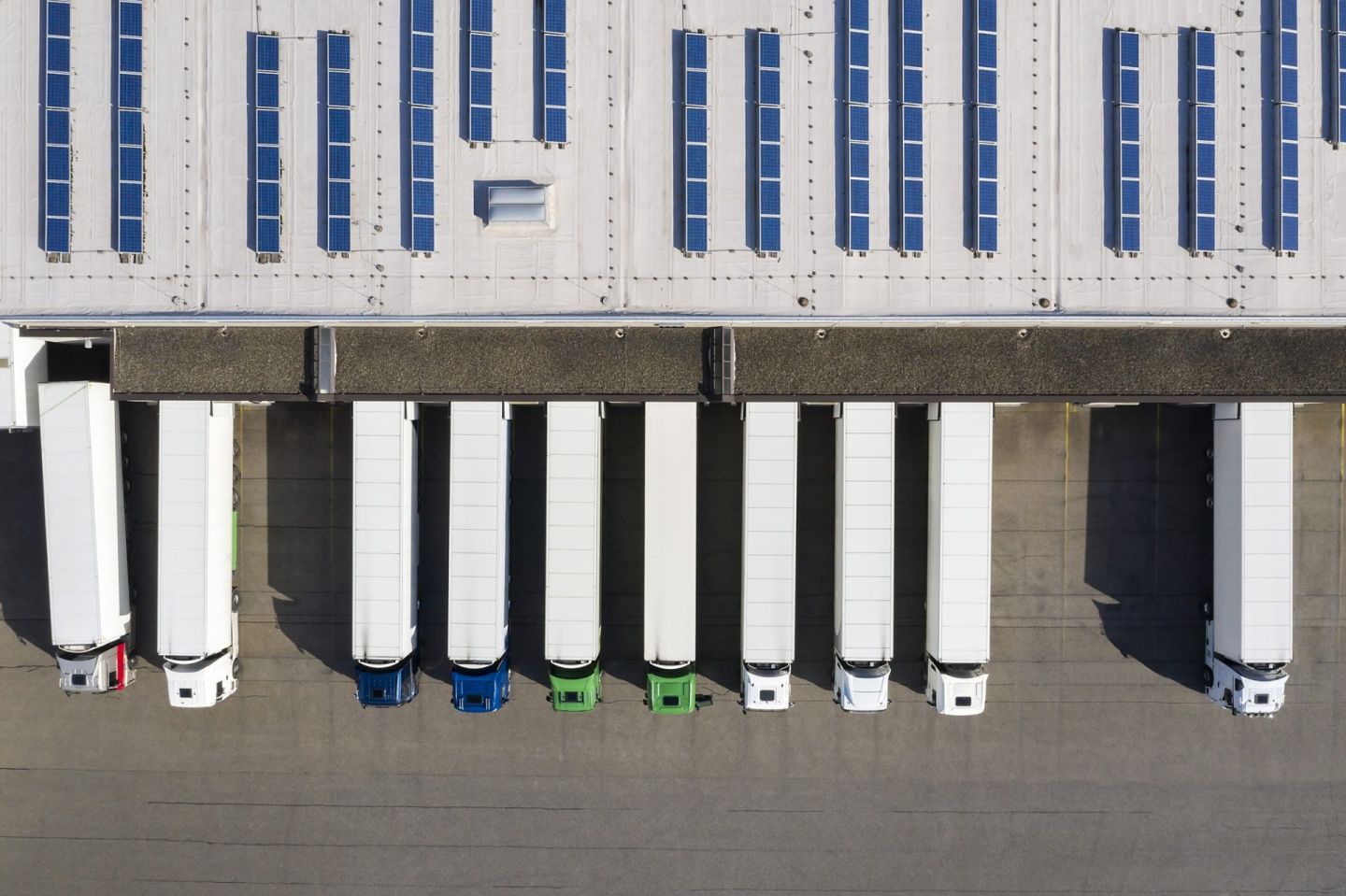
Um das Wachstum zu unterstützen, hat Leroy Merlin 2017 das Projekt „Easylog“ ins Leben gerufen, das auf die Automatisierung des Lagers in Reau abzielt, einem der drei über ganz Frankreich verteilten Standorte, der allein nicht weniger als 140 Geschäfte bedient. Und die Aktivität ist hoch: 1000 Bestellungen pro Tag im B2B-Bereich und 2000 im B2C-Bereich! Konkret handelt es sich bei diesen Aufträgen um Bestellungen zur Auffüllung der Regale in den Geschäften (Selbstbedienungsaufträge), um Kundenbestellungen zur Abholung in den Geschäften (Click and Collect) oder um Internetbestellungen im Rahmen der direkten Lagerlieferung (DWD). Das 72.000 m² große Lager verfügt über 12 Lagereinheiten, von denen 6 (36.000 m²) automatisiert sind.
Nachdem die Einzelhandelskette lange an der Optimierung ihrer Logistik und der Modernisierung ihrer Lagerhäuser gearbeitet hatte, war sie an die Grenzen des traditionellen Modells gestoßen, insbesondere was die Leistung und Sicherheit betraf. Leroy Merlin holte Wavestone mit ins Boot, um das Projekt von Anfang bis Ende zu begleiten, von der Analyse der Verkaufszahlen über die Auswahl der Lösungen bis hin zu deren Umsetzung. Die Leistung wurde in Zusammenarbeit mit 3 anderen Anbietern erbracht: TGW, STILL und AF ERGO CONSEIL. Die Umsetzung der Automatisierung wurde im Juli 2021 abgeschlossen.
Wir sprachen mit Olivier Mangnier, Leiter der Intralogistikprojekte bei Leroy Merlin, um die Ziele dieses Projekts und die zur Erfüllung dieser Ziele gewählten Lösungen zu ergründen.
Warum haben Sie sich für die Automatisierung des Lagers in Réau entschieden?
Unser vorrangiges Ziel war es, die Belastung der Teams bei der Arbeit zu verringern und Arbeitsunfälle so weit wie möglich zu unterbinden. Leroy Merlin ist ein Unternehmen, das Heimwerkerprodukte vertreibt, die oft schwer und sperrig sind. Unser Lagersortiment reicht von Bolzen bis hin zu Arbeitsplatten (Fliesen, Möbel, Garten). Wir wussten, dass wir auch im Zuge der Automatisierung immer Mitarbeiter an den verschiedenen Arbeitsplätzen brauchen würden. Daher war es äußerst wichtig, die Ergonomie dieser verschiedenen Arbeitsplätze zu verbessern.
Zweitens wollten wir unsere Schwierigkeiten bei der Personalbeschaffung überwinden. Da unser Bewerberpool begrenzt ist, wirkt sich dies auf unsere Organisation aus und kann es schwierig machen, unser Kundenversprechen einzuhalten. Wenn wir dank der Automatisierung produktiver werden und weniger Personal benötigen, wollten wir auch eine Lösung, die es uns ermöglicht, auf dem Arbeitsmarkt attraktiver zu sein, denn die Automatisierung vermittelt das Bild einer modernen, qualitativen, durchdachten und angepassten Arbeitsumgebung.
Schließlich suchten wir ein System, das in der Lage ist, Spitzenlasten zu bewältigen und sich an die Verwaltung unterschiedlicher Arbeitsabläufe anzupassen. Die Lösung musste flexibel und leistungsfähig sein, um das Ziel der Omnichannel-Nutzung zu erreichen. So gelangen die Produkte bei B2B vom Lager in den Laden, bei B2C in den Laden zur Abholung oder Lieferung an den Kunden oder direkt zum Kunden nach Hause.
Warum haben Sie für die Durchführung dieses Projekts eine Beratungsleistung in Anspruch genommen?
Es handelte sich um ein umfangreiches Projekt über einen Zeitraum von vier Jahren und wir hatten weder die internen Kompetenzen noch die verfügbaren Teams, um unsere Ziele zu erreichen. Wavestone begleitete uns nicht nur bis zur Einführung, sondern hatte bereits Erfahrung mit mehreren Projekten dieser Art und half uns dabei, herauszufinden, welche Technologien für unseren Bedarf am besten geeignet wären, und die Anbieter auf dem Markt zu sondieren.
Welche Lösungen wurden gewählt, um die Ziele Flexibilität und Leistung zu erreichen?
Die größte Herausforderung bestand darin, eine permanente, aber entwicklungsfähige Lösung für die Warenströme zu haben, die mit dem Wachstum von Leroy Merlin Schritt halten konnte. Da sich die Abläufe ständig ändern, musste die Lösung auf diese Veränderungen reagieren können. Aus diesem Grund entschieden wir uns für ein GTP Shuttle (automatisches Shuttle-Lagersystem), das Behälter zweier unterschiedlicher Größen und somit eine Einzel- und Paketkommissionierung über ein einziges zentrales System bewältigen kann. Wenn eine hohe Nachfrage nach einer Vorbereitungsart auftritt, kann das System die Anzahl der Behälter nach oben oder unten skalieren und auf diese Aktivitätsspitze reagieren.
Für die Warenein- und -auslagerung in den Gängen wurde das FTF-System (Fahrerloses Transportfahrzeug) des Anbieters STILL gewählt. Mit 30 Robotern in Betrieb ist dies der größte Einsatz dieser Lösung in Frankreich.
Die Anlage wird schrittweise entsprechend der zunehmenden Last installiert und ist sowohl nach oben als auch nach unten skalierbar. Dieses automatisierte System bearbeitet sowohl Lagerpaletten als auch Einzelhandelsbestellungen.
Vor welchen Herausforderungen standen Sie und wie haben Sie diese gemeistert?
Unsere Partner TGW und STILL mussten maßgeschneiderte und möglichst kompakte Lösungen schaffen, die in das bestehende Gebäude integriert werden konnten. Unter anderem wurden Zwischengeschosse eingezogen, um die Systeme übereinander stapeln zu können.
Eine weitere Herausforderung: Das Projekt lief während einer Ausnahmesituation, da zwei der vier Jahre von der Pandemie betroffen waren. Trotzdem gerieten wir nur zehn Wochen in Verzug. Das ist bemerkenswert, ja sogar überragend.
Wie gingen Sie auf das Ziel der ergonomischen Gestaltung von Arbeitsplätzen ein?
Dieses Projekt war in erster Linie eine Innovation, die unseren Teams zugutekommen sollte, damit sie in einem qualitativ hochwertigen und sicheren Umfeld arbeiten können.
Wavestone schlug vor, mit AF ERGO CONSEIL zusammenzuarbeiten, um umfangreiche ergonomische Arbeiten unter Einbeziehung der arbeitsmedizinischen Abteilung durchzuführen. Um den berechtigten Befürchtungen der Mitarbeiter (Angst vor dem Verlust ihres Arbeitsplatzes, vor einem Standortwechsel) zu begegnen, wurden die Mitarbeiter bereits in einem sehr frühen Stadium des Projekts einbezogen, damit sie die Entscheidungen, die sich auf sie auswirken würden, verstehen und mittragen konnten.
Alle Teams besuchten Lager, die bereits automatisiert waren, und beteiligten sich dann an der Gestaltung ihrer neuen Arbeitsplätze durch 3D-Simulationen und virtuelle Realität. Diese Einbeziehung im Vorfeld erleichterte die Bewältigung des Wandels und die Akzeptanz der neuen Arbeitsmethoden durch die Mitarbeiter erheblich. Dieser Ansatz wurde von unseren Teams sehr geschätzt.
Welche Bilanz ziehen Sie aus diesem Projekt?
Nach einem Jahr Betrieb können wir folgende Fortschritte und Ergebnisse vorweisen: eine Reduzierung der Bearbeitungskosten für die logistische Lagereinheit um 11 %, eine Reduzierung der Bearbeitungskosten für die Kommissioniereinheit um 15 %, eine zuverlässige Bestandsführung mit einer Fehlerquote von weniger als 0,07 %, eine Fehlerquote bei der Kommissionierung von nahezu 0 % und die Fähigkeit, Spitzenbelastungen mit einem Steigerungspotenzial von mehr als 20 % zu bewältigen (55.000 Produktentnahmen aus dem Lager pro Tag im November).
Aber abgesehen von diesen zufriedenstellenden Zahlen dürfen wir nicht vergessen, dass dies in erster Linie ein menschliches Projekt ist. Wir haben unser erstes Ziel erreicht: In mehr als einem Jahr Betrieb hatten wir fast keine Arbeitsunterbrechungen. Darauf können wir wirklich stolz sein, denn mit einer Häufigkeit von nahezu Null sind wir weit von der Quote von 55 in unserem Verteilungsnetz entfernt.
Der Erfolg dieses Projekts beruht auch auf der Einbindung unserer Teams von Anfang an: vierteljährliche Infoveranstaltungen, dynamische Kommunikation, Besuche von vollständig automatisierten Standorten, Teilnahme an Design-Workshops, Tests und Virtual Reality.
Dies war auch eine Gelegenheit für die Teams, sich durch Vielseitigkeit weiterzuentwickeln, da durch Wechsel des Arbeitsplatzes im Arbeitsalltag ihre Kompetenzen erweitern und neue Berufe erlernen können: Supervisoren, Datenzertifizierer, Ablaufsteuerung, Wartungstechniker. Diese Maßnahmen haben auch dazu geführt, dass mehr Stellen für Frauen geöffnet wurden: Sie machen nun mehr als 30 % der Belegschaft aus, während wir zuvor nahe bei 0 lagen.
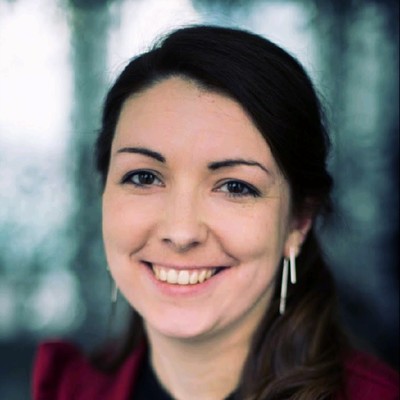
Die gute Zusammenarbeit zwischen allen Beteiligten und die positive Einstellung aller haben mich während des Projekts besonders beeindruckt. Genau dieses Vertrauensverhältnis, das sich zwischen uns entwickelt hat, ist meiner Meinung nach der Schlüssel zum Erfolg des Projekts. Die Wavestone-Teams arbeiteten tagtäglich gerne mit Leroy Merlin, TGW, STILL und AF ERGO CONSEIL zusammen.