Leroy Merlin is automating their storage for the benefit of their teams and performance
- Supply Chain
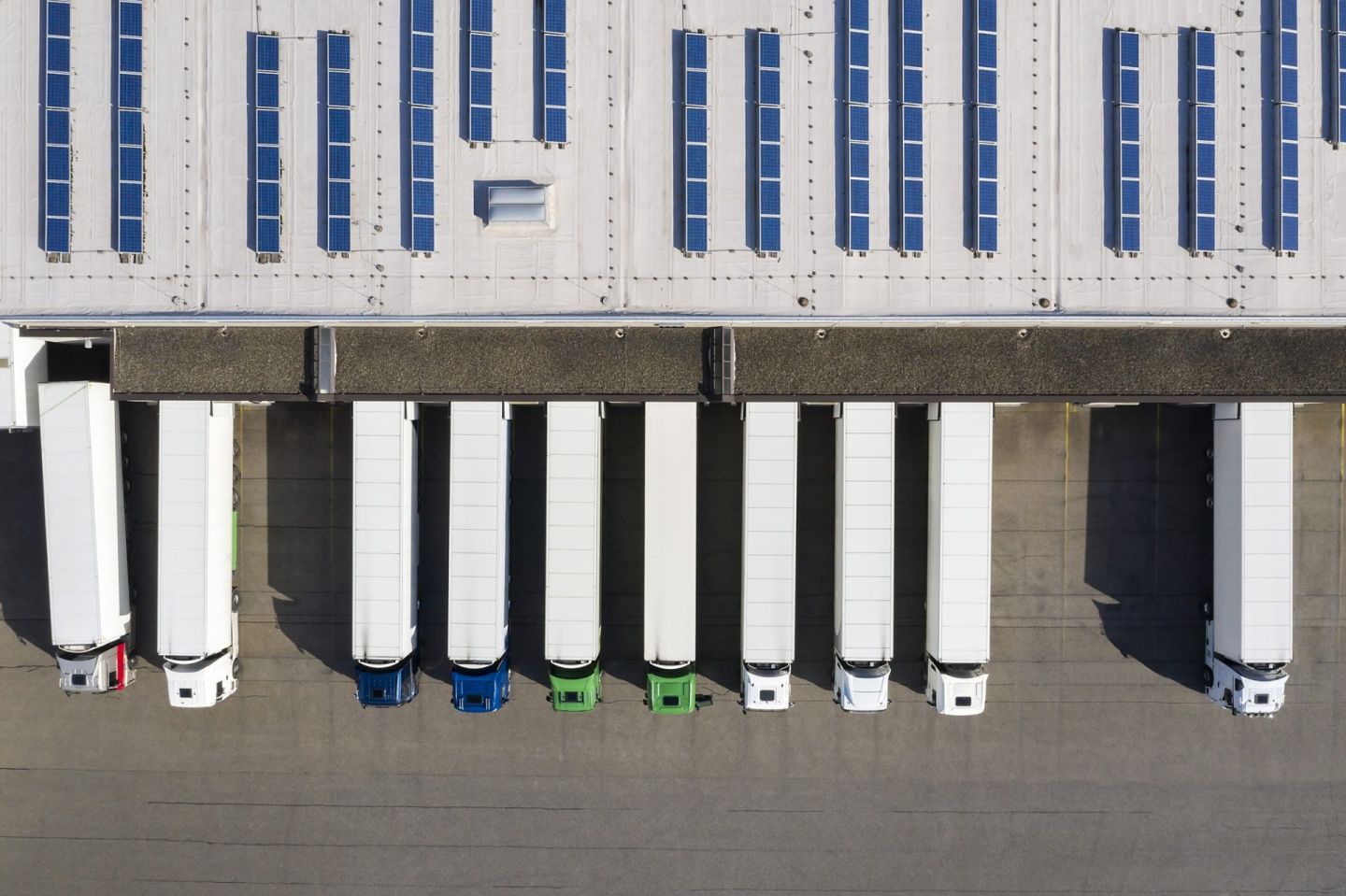
To support their growth, Leroy Merlin launched the “Easylog” project in 2017, which aims to automate the Reau warehouse, one of the three sites spread across France and which by itself serves no less than 140 stores. And its activity is intense: 1000 orders per day in B2B and 2000 in B2C. In concrete terms, these orders can be requests to restock store shelves (self-service orders), customer orders to be picked up in store (click and collect), or web orders in Direct Warehouse Delivery (DWD). The 72,000 m² warehouse has 12 storage cells, 6 of which (36,000 m²) have been automated.
After working for a long time on improving its logistics and modernizing its warehouses, the company had reached the limits of the traditional system, particularly in terms of performance and security. Leroy Merlin asked Wavestone to support them from A to Z on the project, from analyzing their sales, to choosing solutions, to deploying said solutions. The service was carried out in collaboration with 3 other service providers: TGW, STILL and AF ERGO CONSEIL.
We interviewed Olivier Mangnier, Director of intralogistics projects at Leroy Merlin, to understand the objectives of this project and the solutions chosen to address them.
Why did you decide to automate the Réau warehouse?
Our first objective was to reduce the workload of the teams and to eliminate, as much as possible, work-related accidents. Leroy Merlin is a distributor of hardware products which are often heavy and bulky. Our range of stocked products ranges from bolts to worktops (tiles, furniture, garden). We knew that we would always need people at the various workstations, even with automation. Improving the ergonomics of these different workstations was therefore of prime importance.
Secondly, we wanted to overcome our recruitment difficulties. As our applicant pool is limited, this impacts our organization and can make it difficult to keep our customer promise. If mechanization allows us to be more productive and requires fewer human resources, we also wanted a solution that would allow us to be more attractive on the job market because mechanization sends out an image of modernity, of a qualitative, thoughtful, and adapted work environment.
Finally, we wanted a system capable of handling peaks in activity and adapting to the management of varied flows. The flexibility of the solution and its performance were important to meet the objective of omnicanality. The products go from the warehouse to the store for B2B, to the store for B2C with customer pick-up or delivery, or to the customer at home.
Why did Leroy Merlin decide to ask Wavestone to support them?
This was an extensive 4-year project and we did not have the in-house skills nor the teams available to meet our objectives. Wavestone, in addition to accompanying us through to deployment, already had experience with several projects of this type and helped us to know what the best technology would be to meet our needs, and to interview the suppliers on the market.
What solutions have been chosen to meet the objectives of flexibility and performance?
The main challenge was to have a permanent but evolving handling solution to accompany Leroy Merlin’s growth. The solution had to be able to respond to these changes as the flows were constantly evolving. Therefore, we chose a GTP shuttle (automated shuttle storage system), capable of managing two different sizes of bins and therefore of preparing retail and parcel goods on the same centralized system. If there is a high demand for a type of preparation, the system can increase or decrease the number of bins and respond to this peak in activity.
For the storage and removal of products in the aisles, the AGV system (Automatic Guided Vehicle – see image on the right) from the STILL service provider has been chosen. With 30 robots in circulation, this is the largest deployment of this solution in France.
A progressive installation of the latter is planned according to the increase in load and this installation is scalable upwards and downwards. This mechanized system handles both stock pallets and retail orders.
What challenges have you faced and how did you overcome them?
Our partners TGW and STILL had to design solutions in a compact way to fit into the existing building. For example, mezzanines were put in place to stack the different systems.
Another challenge: the project lasted 4 years, including 2 in the middle of the pandemic. And yet, we were only ten weeks behind schedule. This is remarkable, even exceptional.
How did you meet the objective of workstation ergonomics?
This project was first and foremost an innovation for the benefit of our teams, to enable them to work in a qualitative and secure environment.
Wavestone recommended working with AF ERGO CONSEIL to carry out extensive ergonomic work with the involvement of the occupational health department. To address the legitimate fears of operators (fear of losing their jobs, of changing sites), employees were involved at a very early stage of the project in order to understand and take part in the decisions that would impact them.
All the teams visited warehouses that had already been automated and then participated in the design of their new workstations through 3D simulations and virtual reality. This upstream involvement greatly facilitated the management of the change and the acceptance of the new working methods by the operators. The approach was very much appreciated by our teams.
What is your overall appreciation of this project?
After one year of operations, we are experiencing progress and results: an 11% drop in the processing cost of the storage logistics unit, a 15% drop in the processing cost of the preparation unit, a reliable stock with less than 0.07% error rate, a preparation error rate close to 0 and capacity to pass activity peaks with a potential for an expansion of more than 20% (55,000 product withdrawals from the stocks per day in November).
But beyond these satisfying figures, we are keeping in mind that this a human project first of all. We have met our first objective: in more than a year of operation, we have had almost no work stoppages. This is a real source of pride, since with a frequency rate close to zero, we are far from the rate of 55 in our distribution network.
The success of this project also depends on the involvement of our teams from the outset: quarterly information meetings, dynamic communication, visits to mechanized sites for 100% of the teams, participation in design workshops, tests and virtual reality.
This has also been an opportunity for the teams to develop through versatility, as changing workstations during the day allows them to develop their skills and learn new jobs: supervisors, data certifiers, flow controllers, maintenance technicians. These actions have also enabled us to open up more positions to women: they now represent more than 30% of the workforce, whereas before, we were close to zero.
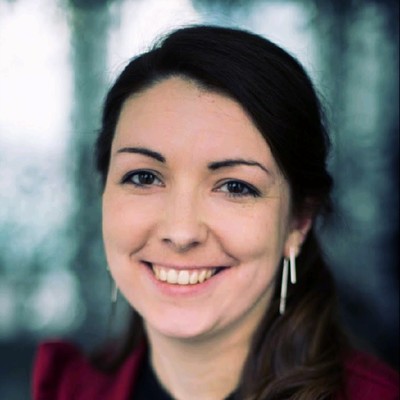
The spirit of collaboration between all the parties involved and the positive attitude of each of them particularly impressed me. It is the relationship of trust created between us that, in my opinion, is at the heart of the project’s success. On a day-to-day basis, the Wavestone teams were happy to work with Leroy Merlin, TGW, STILL and AF ERGO CONSEIL.