Quick wins : comment optimiser les coûts et les délais sur votre site logistique ?
Publié le 14 mai 2024
- Supply Chain
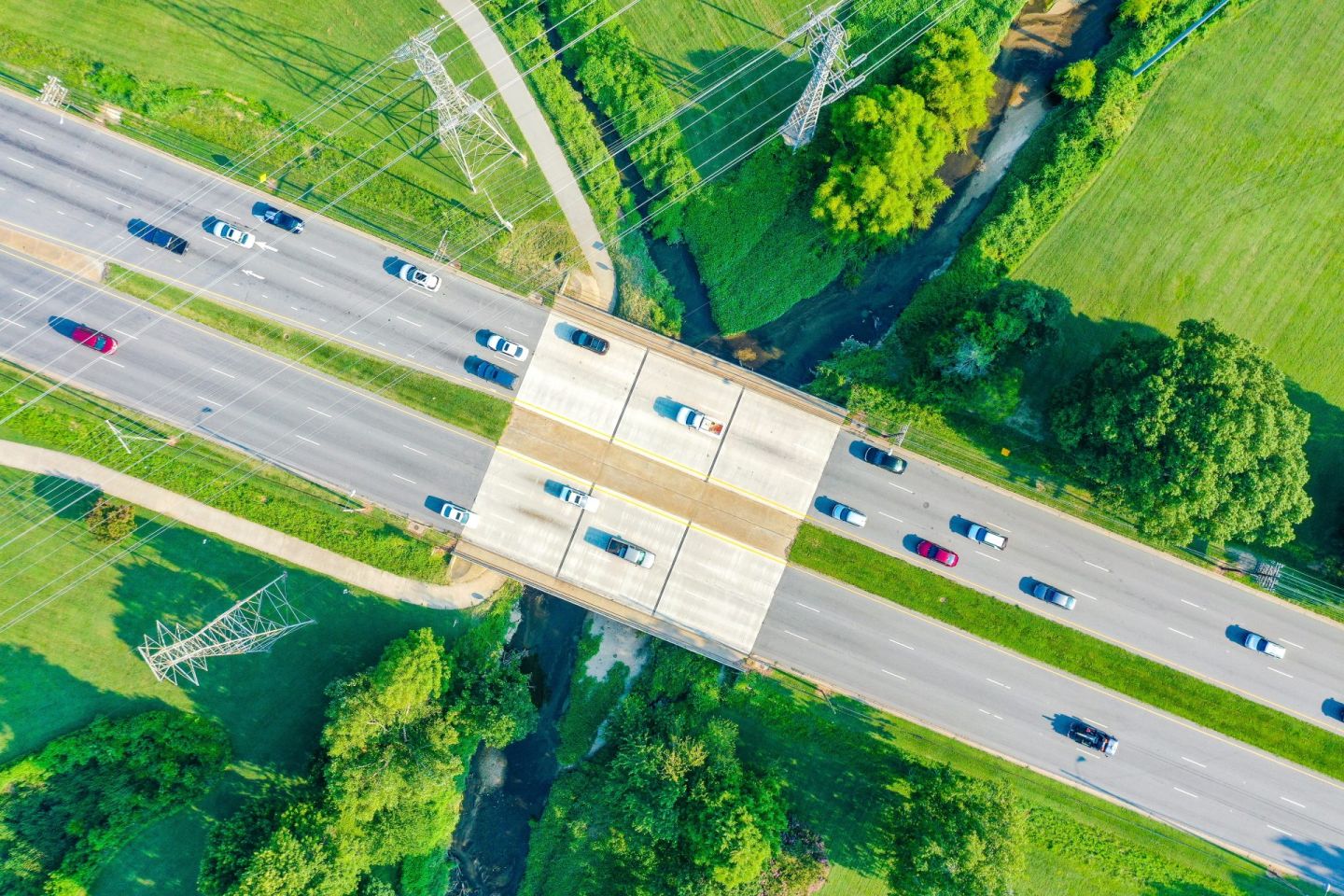
Un guide complet, du diagnostic à la mise en œuvre de solutions
L’intralogistique, qui est un facteur clé de la performance de la supply chain, a considérablement évolué ces dernières années. De l’essor du e-commerce à l’augmentation de la demande en volumes et à la nécessité de livraisons plus rapides, l’activité a progressivement évolué de processus manuels à des processus plus automatisés. Aujourd’hui, la tendance accrue à l’automatisation ne se limite pas à des questions d’efficacité, mais vise également à améliorer l’ergonomie des postes de travail et à permettre aux employés de se consacrer à des tâches à plus forte valeur ajoutée. Cependant, la logique qui plaide en faveur de ces investissements se heurte à un contexte économique instable.
Lorsque les prévisions commerciales sont incertaines, cela peut devenir problématique pour les entreprises de se lancer dans des projets d’automatisation n’ayant des retours sur investissement qu’à long terme. Pour autant, les évolutions les plus récentes en matière de technologie et de services (location d’équipements, solutions SaaS dédiées à la logistique IT, etc.) offrent de nouvelles solutions, flexibles et modulables, permettant de faciliter une approche de l’automatisation plus progressive et moins coûteuse en capital.
Si vous cherchez à évaluer votre intralogistique dans la perspective de l’automatiser, mais que l’investissement dans un projet de grande envergure vous semble prématuré, ce guide des bonnes pratiques est fait pour vous. Réalisé en collaboration avec le Lab Digital & Technologies de France Supply Chain, il vous offre des perspectives facilement applicables et vous présente différents systèmes automatisés ne requérant que peu de ressources pour être déployé. Ce guide vous aidera à manœuvrer dans votre exploration de l’intralogistique, avec des solutions concrètes, rapides et efficaces à mettre en œuvre.
L’article a été écrit grâce aux contributions de logisticiens, de fabricants, de prestataires de service, d’équipementiers et de consultants, chacun apportant leur expertise sur le défi de l’automatisation.
Ce guide suit une méthodologie structurée pour relever les défis de l’intralogistique en trois étapes clés :
- Principes de diagnostic : Évaluer les systèmes de logistique existants, qu’ils soient automatisés ou manuels, pour identifier les points faibles et les pistes d’amélioration.
- Les 3 phases pour un diagnostic précis : De la prise en main à l’identification des points faibles, jusqu’à l’élaboration d’un plan d’action.
- Stratégies opérationnelles pour des résultats rapides et efficaces : isoler les opportunités où l’automatisation peut offrir des gains rapides, pour un investissement inférieur à 1 million d’euros dans un délai d’un an.
1 – DIAGNOSTIC : DE L’ANALYSE APPROFONDIE AUX SOLUTIONS
Le diagnostic logistique de la chaîne d’approvisionnement de votre entrepôt consiste à analyser des différents processus internes et externes de ce dernier, ainsi que leur niveau de performance, leur état et leurs caractéristiques spécifiques. Ceci, pour vous permettre d’identifier les points de faiblesse de votre entrepôt, que celui-ci soit automatisé ou non, afin d’en déterminer les axes potentiels d’amélioration.
Le diagnostic logistique intervient une fois que le site est conçu et opérationnel. Il n’a pas pour but de réexaminer votre stratégie logistique (nombre d’entrepôts, leurs emplacements, choix des circuits de distribution, etc.) ni les solutions techniques adoptées (surface du site souvent prédéfinie, avec ses propres contraintes). La première étape clé consiste à définir le périmètre du projet. Cela implique de cibler le nombre d’entrepôts ou de processus à examiner, ainsi que les lignes de produits ou les canaux de distribution concernés. Pour clore cette première étape d’initialisation, nous identifierons les paramètres susceptibles d’influencer la feuille de route, tels que le niveau attendu de ROI, le calendrier de mise en œuvre ou la durée totale de la mission.
L’objectif d’un diagnostic est de définir un plan d’action pour améliorer la performance coût/service de votre site, à court et moyen terme. Toutefois, ceci implique un large éventail d’actions, allant de votre promesse client spécifique (BtoB ou BtoC), aux ressources et opérations logistiques, en passant par la gestion de l’approvisionnement, de la demande et des achats, ainsi que de l’organisation et des indicateurs de performance.
Une fois les performances réelles de l’entreprise évaluées, elles sont ensuite comparées à celles des principaux concurrents. Un benchmark est réalisé directement sur le terrain, identifie les bonnes pratiques et définit votre promesse client future ou souhaitée.
Une fois le diagnostic logistique terminé, les solutions sont identifiées pour chaque problème mis en évidence lors de l’analyse, ainsi que pour les défis, les risques et les impacts associés. L’étape finale consiste alors à clarifier les priorités et à élaborer une feuille de route pour mettre en œuvre les actions retenues.
Le Lean Management
Il s’agit d’un concept de production applicable aux organisations logistiques, qui se concentre sur la réduction des ressources (y compris le temps) impliquées dans un processus commercial complet. Ceci conduit à supprimer toutes les étapes qui ne génèrent pas de valeur ajoutée dans les opérations.
Cartographie des valeurs : Il s’agit d’une analyse étape par étape d’un processus qui repère et supprime les tâches qui n’apportent pas de valeur ajoutée.
Flexibilité : Des périmètres polyvalents pour des collaborateurs aux compétences multiples, associés à des processus flexibles et de plus en plus automatisés pour gérer des volumes de flux très variables.
Le Takt Time : Synchronisation du rythme des opérations de l’entrepôt avec la demande réelle.
La Méthode 5S : Système d’organisation développé spécifiquement pour façonner un environnement de travail adapté à la logistique allégée.
2. LES TROIS PHASES D’UN DIAGNOSTIC PRÉCIS
Une approche diagnostic typique en 3 trois phases, qui dure généralement entre trois et quatre mois.
Dans la Phase 1, qui s’étend sur un mois environ, l’accent est mis sur l’appropriation, impliquant une immersion totale dans l’environnement de l’entrepôt afin d’en comprendre les processus existants. Ceci est réalisé grâce à la combinaison d’études de terrain (incluant des visites et des entretiens), et des approches quantitatives (analyse de données et de coûts, benchmark et les meilleures pratiques). Les analystes prennent en main le projet, compilant diverses sources d’information, pour une meilleure compréhension des processus de l’entrepôt. La performance est évaluée par le biais d’indicateurs clés issus des données de l’entrepôt, et par une analyse d’aspects comme la gestion des flux, l’utilisation de l’espace et le personnel sur place. Les enquêtes de terrain, et les échanges avec les équipes opérationnelles, sont indispensables pour obtenir des informations que l’analyse statistique seule ne peut révéler, telles que les activités non-conformes, les colis égarés, les blocages de convoyeurs, l’encombrement des allées, etc. Ces éléments contribuent à dresser un tableau détaillé de la situation. L’analyse des coûts et le benchmarking, réalisés à la fois en interne par rapport aux performances passées et aux objectifs, et à l’externe en comparant les bonnes pratiques du marché, sont ensuite utilisés pour détecter ou confirmer les causes d’inefficacité opérationnelle.
La Phase 2 est celle du diagnostic effectif et dure généralement un à deux mois selon la complexité de la situation initiale. Nourrie par les données et les analyses collectées pendant la phase d’appropriation, l’évaluation est présentée autour de quatre axes principaux :
- Coûts logistiques et de transport : cela inclut l’évaluation de la productivité, les taux de remplissage, les coûts fixes et les taux intérimaires.
- Flexibilité et gestion du risques : Ici, l’accent est mis sur le niveau de dépendance de la performance par rapport à l’organisation du transport, par rapport à l’équilibre entre les opérations B2B et B2C.
- Qualité : Cela comprend la mesure du taux d’erreur, les taux de casse ou de perte d’articles, ainsi que les taux globaux de casse.
- Service : Ceci inclut l’évaluation des temps de préparation ou de livraison, le support à la livraison et le niveau de tri dans l’entrepôt.
Pour chaque dysfonctionnement ou inefficacité constaté dans ces secteurs, des stratégies opérationnelles sont identifiées. Les impacts de ces stratégies sont ensuite évalués, à la fois quantitativement (en termes de gains de temps et de bénéfices financiers), et qualitativement (en prenant en compte les améliorations de la visibilité et des conditions de travail). De plus, le niveau d’investissement requis pour chaque stratégie et le retour sur investissement estimé (ROI) sont également calculés.
La troisième et dernière phase du diagnostic vise à convertir les stratégies opérationnelles en une liste d’actions concrètes à réaliser répondant à l’ensemble des enjeux du projet. Pour rationaliser la prise de décisions, ces actions sont notées en fonction de leur potentiel impact (en termes d’efficacité, de qualité, de service, etc), et le temps nécessaire pour obtenir ces résultats.
Ces actions sont ensuite cartographiées dans un schéma mesurant la complexité rencontrée lors de la mise en œuvre, et les délais requis. Les gains rapides réalisables (à fort impact et de faible complexité) sont faciles à identifier, et les actions sont priorisées, sélectionnées et planifiées selon un calendrier de mise en œuvre. Le plan d’action est imaginé pour optimiser l’ensemble de la chaîne d’approvisionnement de l’entrepôt. Les actions peuvent ainsi couvrir tous types d’activités, de la réception des produits à leur expédition, en passant par la gestion des équipes.
Suivi de la performance
Une fois le diagnostic réalisé et les priorités posées, il est essentiel de suivre les performances par rapport aux objectifs fixés. Un ensemble d’outils de suivi peut être mis en place, ou des outils existants peuvent être adaptés pour collecter à la fois des données en temps réel de gestion opérationnelle au quotidien, et un tableau de bord pour suivre les performances et ainsi anticiper les problèmes à venir et les écarts par rapport à la cible.
3. STRATÉGIES OPÉRATIONNELLES D’AUTOMATISATION POUR DES GAINS RAPIDES
Dans notre contexte, un gain rapide se réfère à des initiatives pouvant être déployées avec des ressources limitées mais qui offrent des bénéfices concrets et immédiats pour l’entreprise. Dans l’entrepôt, cela se traduit par des projets dont le coût ne dépasse pas 1 million d’euros, et dont l’exécution peut se faire en moins d’un an.
Des gains rapides en automatisation peuvent être obtenus aussi bien pour des entrepôts non automatisés que pour des entrepôts déjà automatisés. Pour les entrepôts non automatisés, il est possible d’introduire des solutions d’automatisation ne nécessitant qu’un faible investissement de départ et pouvant être exécutée rapidement. Certains systèmes à faibles coûts offrent des avantages dans plusieurs domaines. Les revenus directs sont exprimés en £ (livres sterling).
- Productivité/Rapidité : L’automatisation réduit les délais de traitement des commandes, rationalise les opérations et diminue les coûts de production unitaire. De plus, cela simplifie le suivi pour d’autres améliorations de l’efficacité.
- Qualité du service : La mécanisation réduit les erreurs humaines, augmente la qualité du service et l’efficacité opérationnelle, diminue le besoin de retravailler.
- Conditions de travail : Les systèmes automatisés s’occupent des charges lourdes, permettent d’éviter les postures non-ergonomiques et les longs déplacements, et fonctionnent dans des environnements de travail difficiles (froid extrême, bruit, etc). Ces avancées améliorent les conditions de travail des salariés, réduisant ainsi l’absentéisme et facilitant le recrutement de personnel en diminuant les contraintes physiques.
- Capacité de stockage : L’utilisation des systèmes automatisés permet d’augmenter la capacité de stockage en exploitant l’espace vertical pour les rangements en hauteur ou en profondeur. Ceci facilite la gestion des pics d’activité et optimise la capacité opérationnelle dans les infrastructures existantes.
Dans les entrepôts automatisés, les gains rapides proviennent d’améliorations sans repenser intégralement les systèmes préexistants. Reconnaître les causes profondes d’une chute dans les performances permettent de choisir la solution la plus adéquate pour obtenir des gains rapides. Les problèmes les plus fréquemment rencontrés sont :
- Les niveaux de performance des équipements et des systèmes ne sont pas atteints, ce qui peut provenir d’un flux de colis irréguliers, de points de congestion, de carences sur certains sous-systèmes, d’absence de tampons à des points stratégiques, mais également de la performance des opérateurs ou de pannes d’équipements.
- La répartition et le positionnement des produits dans les espaces de stockage est parfois inadéquat. Pour tirer pleinement parti de la valeur ajoutée de l’automatisation, celle-ci devrait d’abord être utilisée pour traiter les articles de faible volume qui nécessitent plus d’efforts de préparation, plutôt que les produits les plus demandés.
- La détérioration de l’utilisation ou du suivi du système : la gestion des lancements et de l’assortiment des commandes est essentielle dans le contrôle des systèmes automatisés. Les problèmes récurrents sont : des vagues de lancement dont la taille n’est pas compatible avec les zones tampons utilisées, un taux de couverture trop élevé ou trop faible, des prévisions ou des calculs de pré-préparation peu fiables, des règles inadaptées du WCS/WMS ou encore des problèmes d’organisation des équipes.
- Des installations vieillissantes : avec le temps, les systèmes automatisés peuvent présenter des signes de fatigue. La maintenance et la modernisation sont donc primordiales pour rester en phase avec les évolutions de flux. Des problèmes peuvent survenir en raison d’un entretien inadapté, ou de la difficulté à absorber des volumes croissants.
Cette approche implique l’installation, la location ou le financement d’équipement à la demande, avec la possibilité de le relocaliser si nécessaire. Ce modèle, déjà établi dans les secteurs des chariots élévateurs et de l’informatique logistique, est séduisant dans les marchés où les prévisions économiques à long terme sont incertaines. L’utilisation de la technologie se fait à moindre coût avec un risque limité, se concentrant sur des bénéfices immédiats. Des solutions plus élaborées comme le stockage ou le tri automatisés demeurent indispensables pour maximiser le stockage ou l’activité dans des espaces restreints et sont souvent justifiées par les économies sur les constructions. Cette évolution permet aux entreprises de commencer à petite échelle et de moduler, louer ou déplacer l’équipement selon les besoins.
Auteur
-
Lucie Fabre
Manager – France, Paris
Wavestone
LinkedIn